As the first offshore wind projects are established in the U.S., so too are the first American supply chains for turbine design, manufacturing, assembly, and construction.
A growing network of companies are working together to ensure this new clean energy industry is built by and for America. As a result, thousands of jobs are being created, communities are experiencing economic revivals, and our country’s history of skilled manufacturing is taking a much-needed step forward.
In New York, one such story begins with steel and ends on the banks of the Hudson River.

Procured from states like Pennsylvania and Kentucky, steel and other raw materials are the building blocks for turbines that will generate clean, renewable energy for millions of homes and businesses for the next 30-plus years. To make this possible, U.S. manufacturers and fabricators have been mobilized to fill the supply chain, utilizing their expertise and refining their processes to suit this new market. Each company also brings its own far-reaching network, from services like safety equipment and waste removal, to local hotels and restaurants accommodating visitors or out-of-state workers. Such downstream jobs and economic impacts are hard to quantify. They are a quiet addition to the hundreds of more clearly defined coastal manufacturing and construction jobs born from offshore wind projects. Ultimately, this particular network comes together at the Port of Coeymans, where local Tier 1 supplier for secondary steel, Riggs Distler, has again stood up operations, moving with the industry and serving as the nexus between suppliers and Ørsted’s Sunrise Wind (924 MW) project.
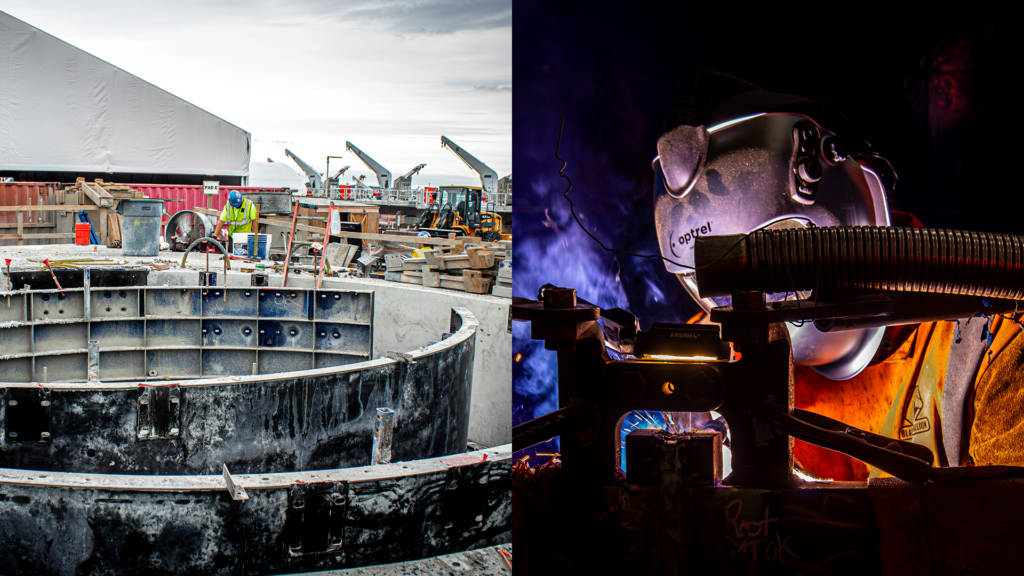
Building these components from start to finish in the U.S. is no easy feat — especially considering the country’s first commercial-scale offshore wind project was just completed this year. To be successful has required commitment from industry, partnership with government, and engagement with local communities. And perhaps above all, patience.
The time and investments have been worth it, supply chain companies told Oceantic Network this summer as part of the U.S. Offshore Wind Jobs Tour. Along the way, our organization captured stories from welding supervisors, C-suite executives, union workers, engineers, and others about how the influx of offshore wind-related work has impacted their jobs, businesses, and neighborhoods. We’ve compiled those takeaways in the video and article below, following the supply chain through New York as it makes its way from America’s heartland, east to the Hudson River, and out to Sunrise Wind 30 miles off the coast Montauk Point, New York.
A Clean Energy ‘Turnaround’
Our story begins in the small, former oil town of Wellsville, New York — located over 300 miles from the Atlantic Coast — at LJUNGSTRÖM’s steel fabrication facility.
For more than 100 years the company has been a major employer for the region, selling steel components to coal-fired power plants. But when the company’s leadership foresaw a decline in their long-held market, LJUNGSTRÖM began investigating opportunities in the renewable energy sector, prompting a business transition and $15 million in facility investments over the last four years.
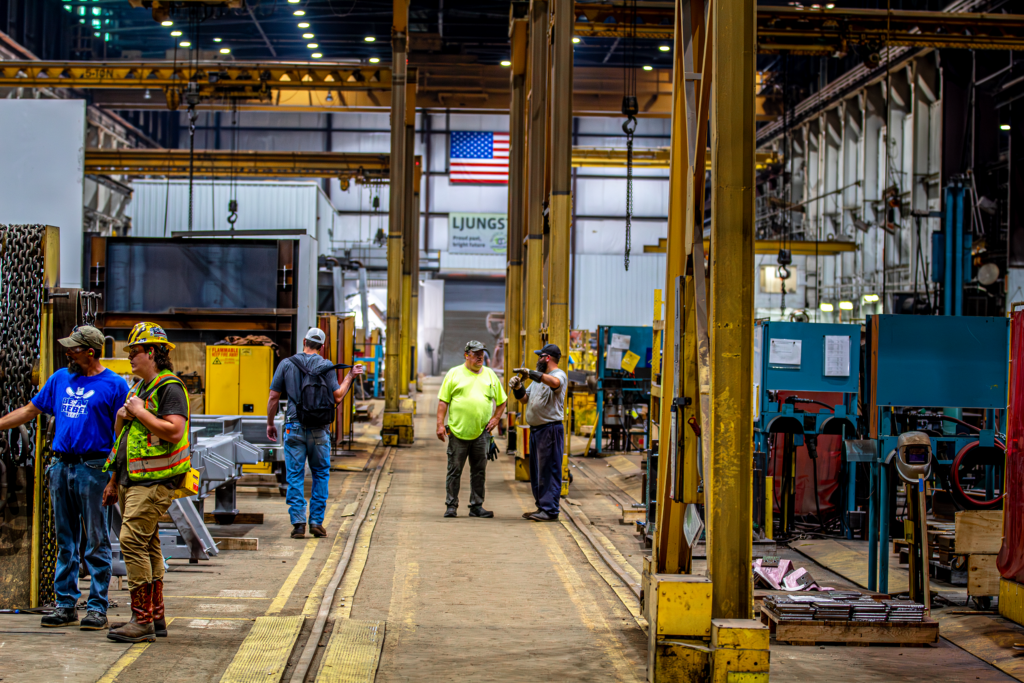
Now, several years into fulfilling offshore wind contracts, the company has expanded its payroll by more than 87% for a total of roughly 375 employees. Many of the facility’s workers are skilled welders supporting the building of advanced foundation components for offshore wind, which include steel anode cages, monopile doors that will be used to access the inside of turbines via a platform, and supported internal platforms (SIPs) that contain many of the electrical components inside the turbine’s monopile. Others specialize in painting and coating operations, which require a climate-controlled room added as part of the recent facility investment. LJUNGSTRÖM provides training such as reskilling former automotive painters and teaching new processes such as flux-core or pulse welding. Furthermore, to ensure the next generation enters the workforce with these skills, the company has helped revamp relevant curriculums at local colleges, trade programs, and grade schools. The economic benefits of LJUNGSTRÖM’s offshore wind contracts have spilled into the town itself, increasing business at local restaurants and hotels. And other states where the company’s up-and-downstream suppliers reside also feel the benefits. LJUNGSTRÖM sources its steel from states including Pennsylvania, Kentucky, Texas, Michigan, and New York, and other supplies from companies in Ohio, Tennessee, Illinois, New Jersey, and Florida.
Prior to working on Sunrise Wind, LJUNGSTRÖM cut its teeth making components for Ørsted’s South Fork Wind (132 MW) and Revolution Wind (704 MW) projects. In total, the company has built and shipped about 150 anode cages to ports in Rhode Island and New York, where they await additional assembly and installation. Fabrication of the SIPs — highly complex, 2,000-plus piece components and the first of their kind to be made in the U.S. — began in 2023 and will continue into 2025.
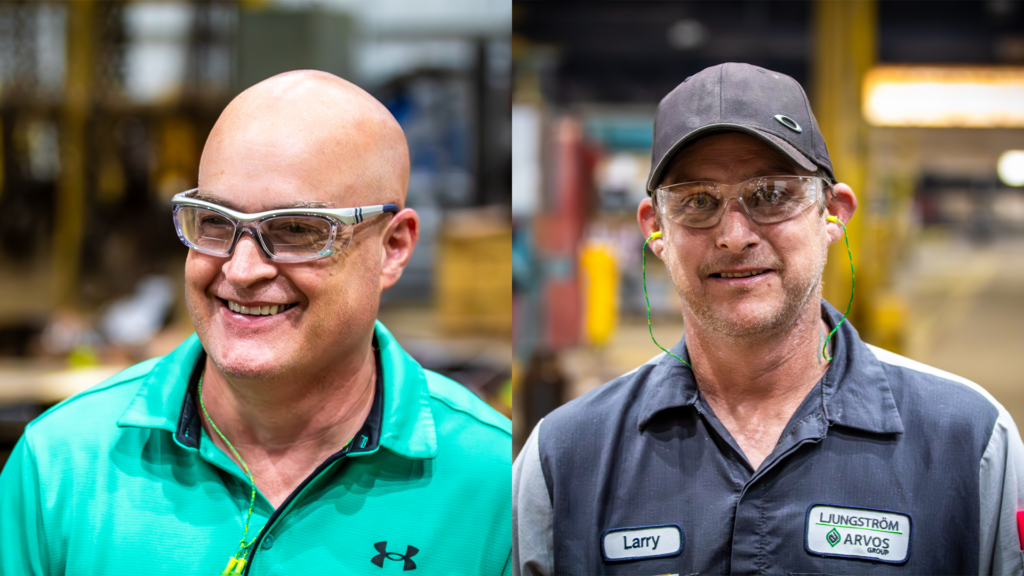
“Offshore wind requires a big space with a lot of administrative staff to keep on top of the requirements,” said Michael Zakel, LJUNGSTRÖM’s Custom Manufacturing Solutions Director. “To get involved, you have to understand your strengths and weaknesses as an organization.”
Today, about 50% of the company’s overall business is offshore wind contracts, and Zakel credits the shift with LJUNGSTRÖM’s “turnaround.” The company is hopeful the next round of state-run offshore wind procurements will lead to more work.
“Ørsted has been our first offshore wind customer, but they won’t be our last,” said Jude Auman, Business Development Manager at the company.
From Rust Belt to ‘Green Belt’
While companies like LJUNGSTRÖM pivoted to offshore wind, others set up operations in New York with the express purpose of serving the new industry.
Technostrobe, which is best known for manufacturing obstruction lights for tall towers, opened its first U.S. operations in Albany, New York with “a 100% focus on offshore wind,” said Technostrobe Offshore Solutions (TOS) Executive Vice President Jeff Grabner.
The company with offices in Europe and Canada jumped at the opportunity to move into the U.S. offshore wind market. Within two years, they outgrew their first space and expanded into a 30,000-square-foot facility, shared with another offshore wind supplier, Lichtgitter USA. The international company produces industrial floor coverings and fiberglass components, among other parts, and Lichtgitter’s General Manager in Albany, Tobias Hornhues, confirmed the manufacturer has also seen “massive growth” in the U.S. market.
Today, TOS has eight associates employed in Albany receiving raw goods, handling inventory, assembling components, and trucking them to the Port of Coeymans for final construction. The company uses an IKEA-style approach to packaging the electrical, lights, railings and other components in a color-coded kit for easy assembly at the port. This helps increase efficiency on the job site and reduce labor costs.
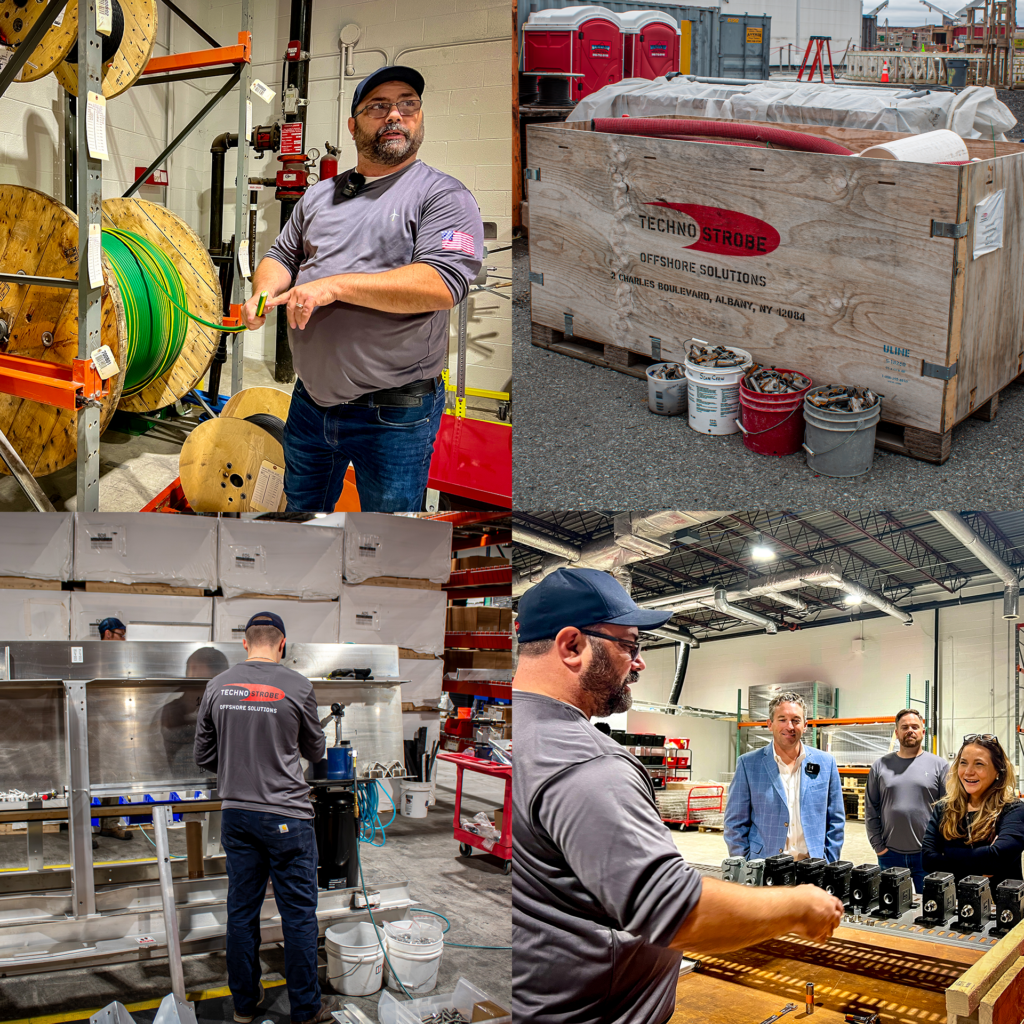
When the company first began working in the U.S., Grabner said it had to lean on European expertise. But with time, experience, and local engagement, TOS has built a supply chain that is over 60% domestic and growing. Goods have been sourced from within New York, Connecticut, and states in the Midwest where Grabner said the company is working to help turn “a rust belt into a green belt.” It’s important work the company has taken on to help identify, cultivate, and develop the U.S. supply chain. By the end of 2024, TOS will have completed products for more than 250 wind turbine generators since beginning operations in February 2022.
“For this industry to succeed, components need to be made, purchased, and sold in the U.S.,” Grabner said. “We’re sharing our story to show the design, engineering, and manufacturing muscle power we already have right here.”
Similar to TOS, another company in the local supply chain, BV Steel Technology, also moved into the region after seeing the great potential of the Albany-area supplier hub. BV Steel’s German parent company set up a small manufacturing operation in Queensbury, New York in 2021.
Under the vision of President Abdul Khail, the company has provided engineering work, as well as embedded parts for turbine transition pieces, SIPs, internal components, and ladder systems for projects including South Fork Wind, Revolution Wind, and Sunrise Wind.

While companies in the New York offshore wind supply chain await the state’s next solicitation, BV Steel has found work in related fields, such as maritime solutions, components for substations, and products for industries such as solar and energy storage. Much of this new work was born out of connections made through the offshore wind industry, notably at Oceantic Network’s annual International Partnering Forum (IPF).
“IPF has been a great portal to get to know other people,” Khail said. “It’s where we keep pushing each other, and where you take the temperature of the industry.”
From BV Steel’s 11,000-square-foot facility, Khail said he and his two employees can be “quick on our feet” and pivot to respond to the new contracts. However, he’d ultimately like to see the pipeline of direct offshore wind work increase so that he can continue to expand the company’s operations in New York. If new contracts do come their way, Khail said he could grow the facility’s employee count and footprint.
Local Labor Yields Regional Benefits
LJUNGSTRÖM, TOS, Lichtgitter, and BV Steel all represent spokes of the same wheel — New York companies utilizing their unique expertise and working together as a homegrown supply chain to deliver thousands of critical components to one central point, the Port of Coeymans.
At the port, parts are received by Riggs Distler, a Centuri company, who is one of the largest union utility, mechanical, and electrical contractors in the U.S. Headquartered in New Jersey with offices in New York and beyond, Riggs Distler serves as a Tier 1 supplier for secondary steel and uses a 100% union workforce to complete the advanced foundation components started by LJUNGSTRÖM and added to by other companies in the New York supply chain. Riggs Distler workers are responsible for finalizing the steel anode cages, SIPs, and concrete platforms that attach to the monopiles and allow technicians to work inside the turbines via the monopile doors made by LJUNGSTRÖM.
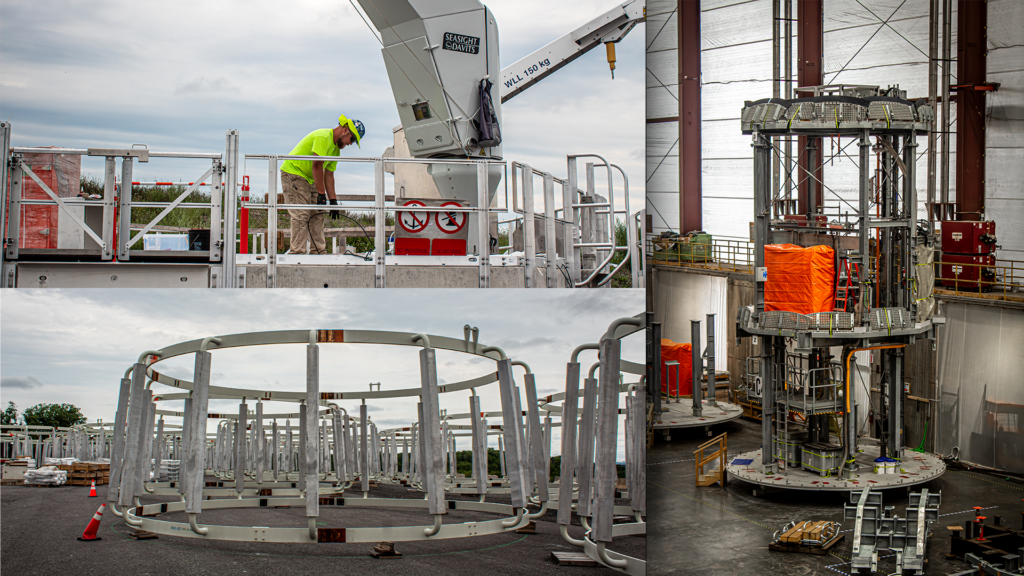
Since creating an offshore wind division in 2021, Riggs Distler and its union workforce have constructed advanced foundation components for three Ørsted projects, South Fork Wind, Revolution Wind, and now Sunrise Wind. Components for the first two projects were handled by a team of roughly 145 employees at ProvPort in Rhode Island. In New York, the company has employed over 125 union craft and 20 staff workers at the Port of Coeymans to complete 84 iterations of each of the three components — one for each turbine in the 924 MW project.
“As we mobilize to different project locations in various states, we have made significant efforts to localize our supply chain to the communities we serve,” said Chris Johnston, VP of Offshore Wind for Riggs Distler, who noted examples such as equipment rentals, tooling, consumables, and engineering support. “This not only benefits our downstream suppliers, but also brings additional economic benefits to the communities we serve.”
Construction activity at the Port of Coeymans began in spring 2023 and has involved bringing on team members from the following unions; Carpenter LU 291, IBEW LU 236, Ironworkers LU 12, Laborers LU 190, Operating Engineers LU 158, and OPCMIA- LU 780 Cement Masons. In many cases, the union workers are hired locally so that, for example, New York ironworkers are welding anode cages in their home state for turbines that will be installed in a project designed to power their state’s homes and businesses. It’s also work that is often quite different from what many long-time union members are accustomed to, providing new skills and experiences that contribute to personal and professional growth and adaptability. Offshore wind demands incredibly high specifications that several individuals described as “one level below aerospace.”
Riggs Distler has also been contracted to complete other types of offshore wind-related work including upgrading four substations in Rhode Island and reconstructing a 13.5-mile 115kV energized line in the state — two projects that will ensure the state can support the new energy to be generated by Revolution Wind. Other companies have taken note of Riggs Distler’s growing expertise. Earlier this year, Vineyard Offshore’s bid included the company as the fabricator and assembler of secondary steel components for its Vineyard Wind 2 project that was recently selected by Massachusetts for further negotiations. The work, expected to take place at ProvPort, could support 150 jobs. Riggs Distler is also the official onshore substation contractor for New Jersey’s Atlantic Shores (~2,800 MW) offshore wind project.
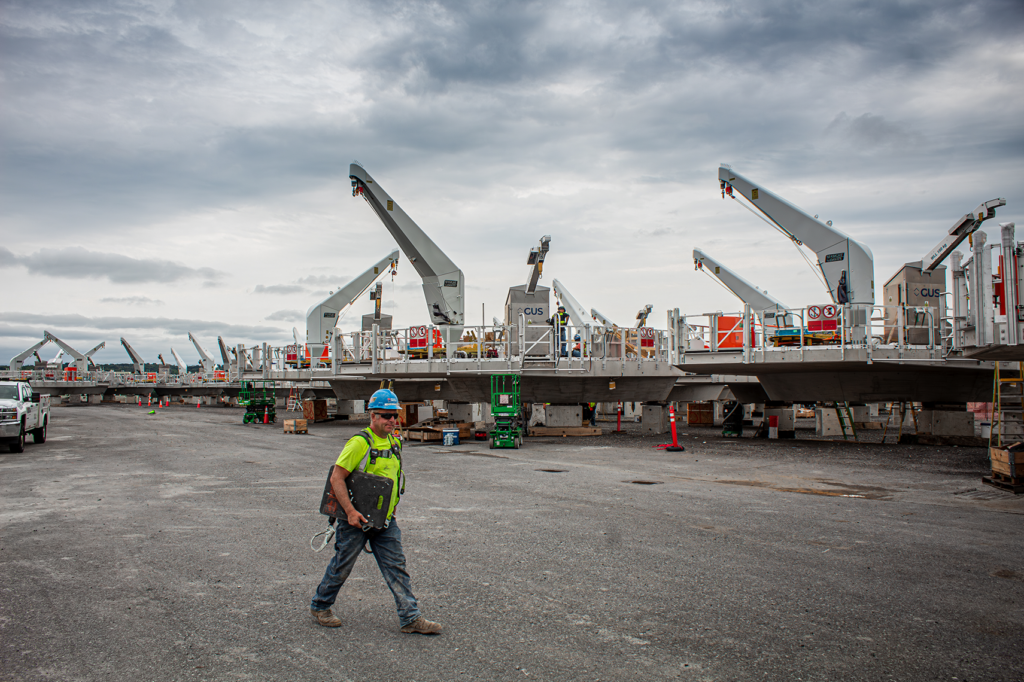
Combined, this work showcases how Riggs Distler seized the opportunity to lead the construction of offshore wind in America, and in partnership with developers such as Ørsted, has helped ensure our new clean energy industry capitalizes on the skilled workers and companies already present here. Bolstered by local content requirements the state incorporated into the agreements signed with developers, New York businesses, communities, and individuals have capitalized on the economic benefits of offshore wind development. Now, it’s up to all of us to keep driving the train forward with new projects, contracts, and opportunities to continue growing our U.S. offshore wind supply chain.
It’s not hard to see, especially looking at New York, that offshore wind is working — and so is America.
Learn more at oceantic.org/jobstour